As the gears of production turn in the manufacturing industry, one critical factor keeps the machinery well-oiled and running smoothly: manufacturing capacity planning.
With the advent of technology, this process has transitioned from a managerial function to a strategic cornerstone that determines the pace and efficiency of production — ultimately affecting your business's bottom line.
But what exactly is manufacturing capacity planning, why is it so crucial in the current production landscape, and how can software improve the process for manufacturing companies looking to grow?
Understanding Manufacturing Capacity Planning
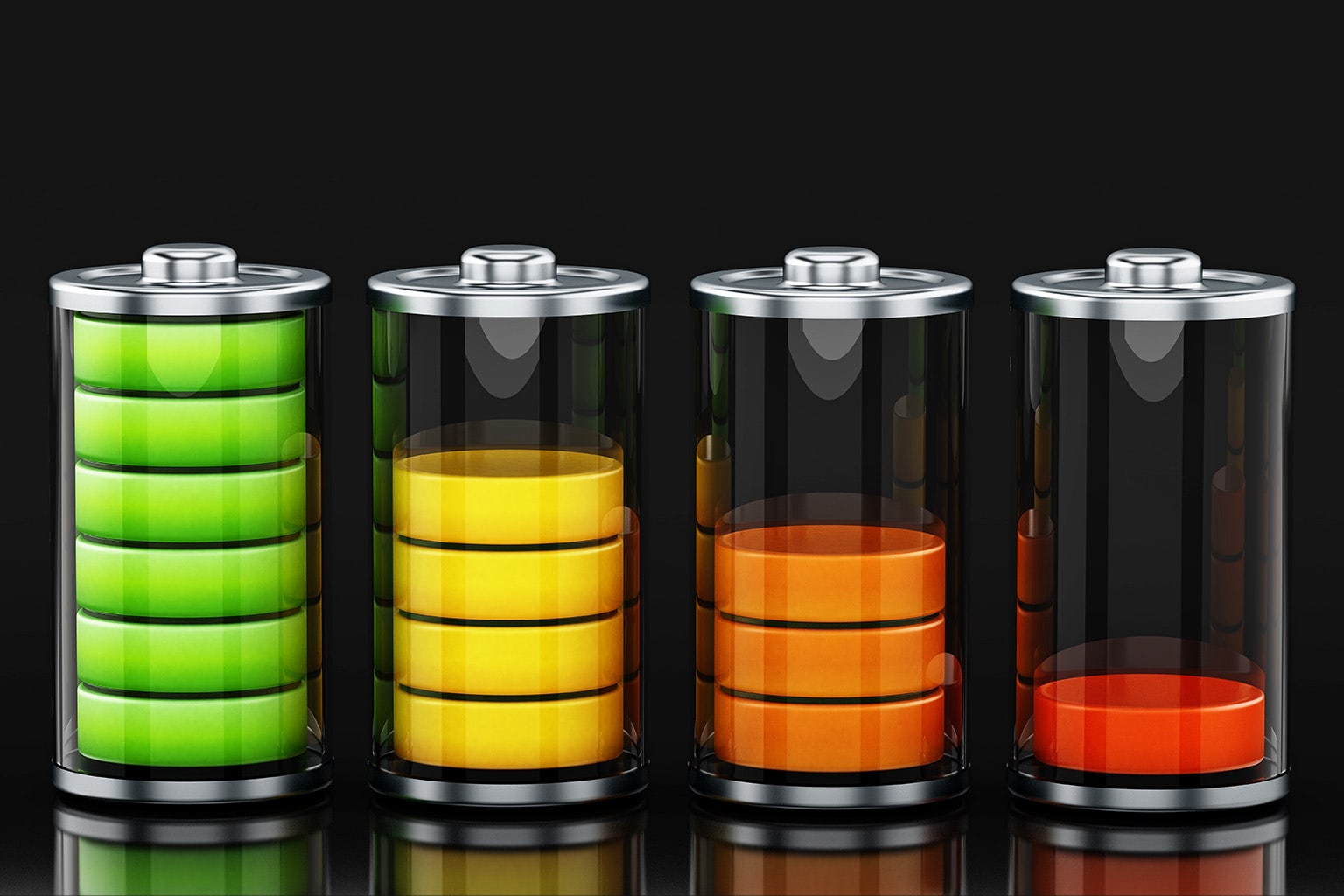
Capacity planning is the strategic process of determining the maximum production rate achievable in a manufacturing facility or on a production line.
It involves analyzing the existing capacity, forecasting future demand, recognizing discrepancies, and formulating a capacity planning strategy to maximize actual output.Â
Capacity planning is like a roadmap guiding a manufacturing business, ensuring it has the right quantity of resources — human, equipment, or product — at the right time to meet customer demand.
Various types of capacity planning include:
- Workforce capacity planning
- Equipment capacity planning
- Production capacity planning
Navigating through capacity planning helps decision-makers manage costs for production against required resources — cost-effectively balancing supply and demand to meet company goals.
{{scorecard}}
The Difference Between Capacity Planning and Resource Planning
Capacity planning and resource planning are two distinct but interconnected concepts in the context of manufacturing and production management.
Capacity planning assesses the organization's ability to handle production volumes within a given timeframe by factoring in machinery, personnel, skill, and speed.
Resource planning, on the other hand, focuses on operational processes like supply chain, warehouse, and inventory management.
3 Types of Manufacturing Capacity Planning
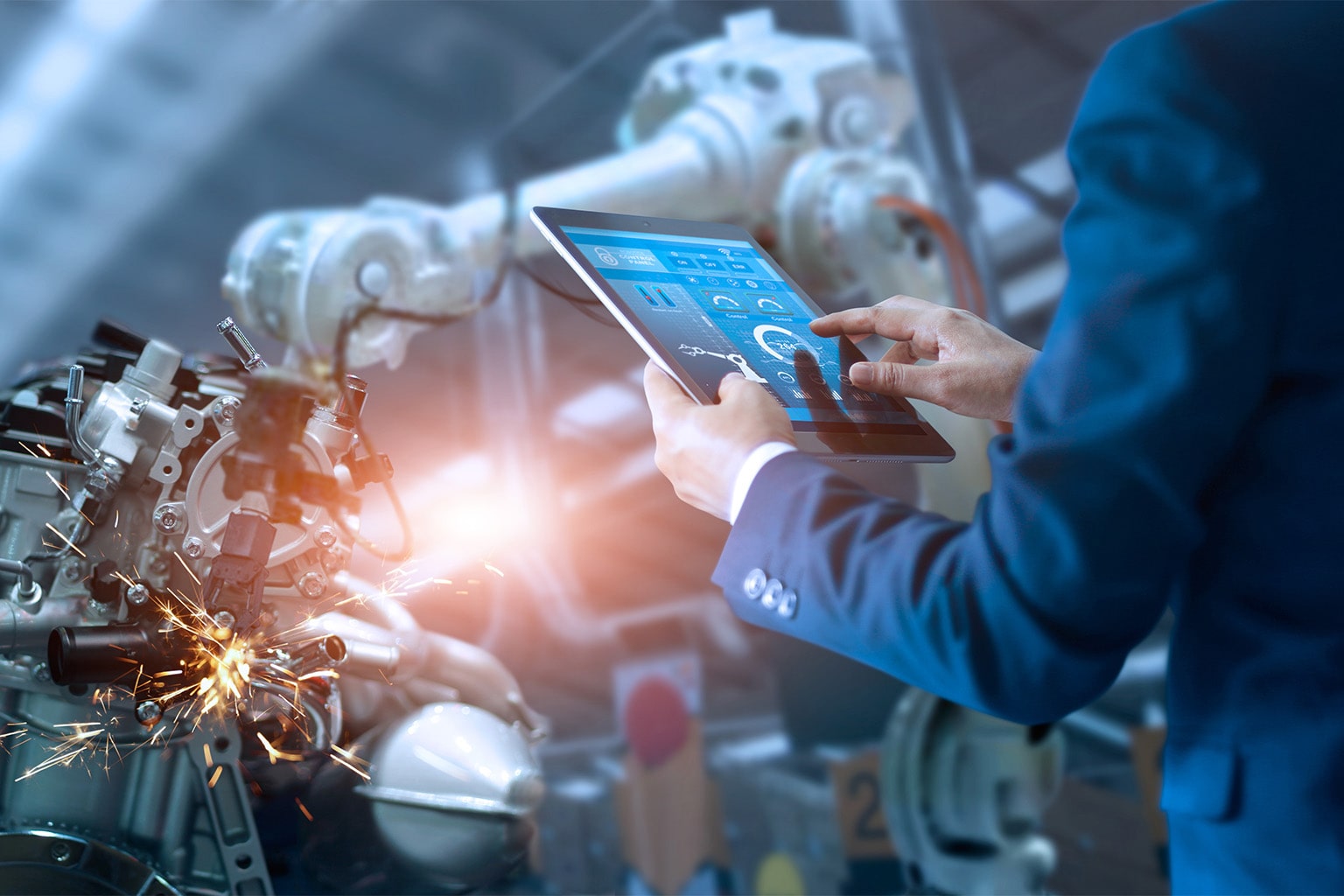
The three essential components of manufacturing capacity planning are workforce, equipment, and product capacity. Each component carries its unique weight in the process, contributing to the overall efficiency and effectiveness of capacity management.
Workforce Capacity Planning
Workforce capacity planning ensures organizations have the necessary personnel and working hours available to fulfill tasks and meet demand.
This involves meticulously evaluating factors like capacity to recruit, onboarding of new personnel, worker productivity, and the projected budget.
Without workforce capacity planning, workers can become overworked if stretched too thin. Tier morale and quality of work can decline, causing poor product quality and increasing manufacturing lead times.
Think of it as a well-choreographed dance, where every dancer (employee) knows their moves (tasks) and timing (working hours). Investing in a platform that offers an overview of shop floor operations is a crucial step in this dance, allowing for efficient and effective workforce capacity management.
Equipment Capacity Planning
Equipment forms the backbone of the manufacturing process. Equipment capacity planning is a method used to determine the maximum production rate achievable at a facility or on a production line.
It analyzes this rate compared to customer orders and anticipated demand and devises a production capacity plan to maximize actual output.
This component considers machine speeds, downtime, maintenance, training, and employee skill sets.
Effective equipment capacity planning can significantly enhance the rhythm of the manufacturing process, decreasing expenses, enhancing efficiency, and increasing customer satisfaction.
It can be challenging to execute equipment capacity planning, even with cutting-edge software like NetSuite (out-of-the-box). However, companies like Champion Fiberglass (partnering with StratusGreen) have been able to thrive by developing solutions like custom preventative maintenance programs to solve for equipment capacity planning.
Product Capacity Planning
Product capacity planning ensures a business has the requisite number of products to fulfill orders. For example, in the automotive aftermarket parts industry, products can include batteries, radiators, and steering wheels that need to be in stock.
This process involves analyzing historical data, forecasting future demand, and making decisions about production levels, reorder points, safety stock levels, utilization, and bottlenecks.
Let’s take a closer look:
- Demand forecasting: To begin the product capacity planning process, manufacturers analyze historical sales data and use statistical methods to forecast future demand.
- Reorder points are determined by the lead time, demand variability, and desired service level. The reorder point helps ensure that production can continue without disruptions or stockouts.
- Safety stock is additional inventory maintained above the expected demand level to buffer against uncertainties. It serves as a contingency for unexpected fluctuations in demand, supply chain disruptions, or production delays.
- Production capacity refers to the maximum output a manufacturing facility can achieve within a given time frame. It considers various factors such as equipment capabilities, labor availability, production efficiency, and plant operating hours.
- Capacity utilization is the ratio of actual production output to the maximum production capacity available.
- Constraints and bottlenecks include equipment limitations, skill shortages, supply chain limitations, or other factors impacting the overall production capacity.Â
To solve for product capacity planning, manufacturers can employ industry-specific platforms like NetSuite to harness features like its Manufacturing Requirements Planning tool.
NetSuite's MRP feature determines what raw materials, components, and subassemblies are needed to build products according to demand and bills of materials (BOMs). You can also plan for hypothetical scenarios to test how certain conditions affect your inventory.
Best of all, NetSuite accesses data from your entire ERP, effectively providing a single source of truth to make confident decisions on scheduling and production calculations.
Understanding Finite and Infinite Capacity Planning
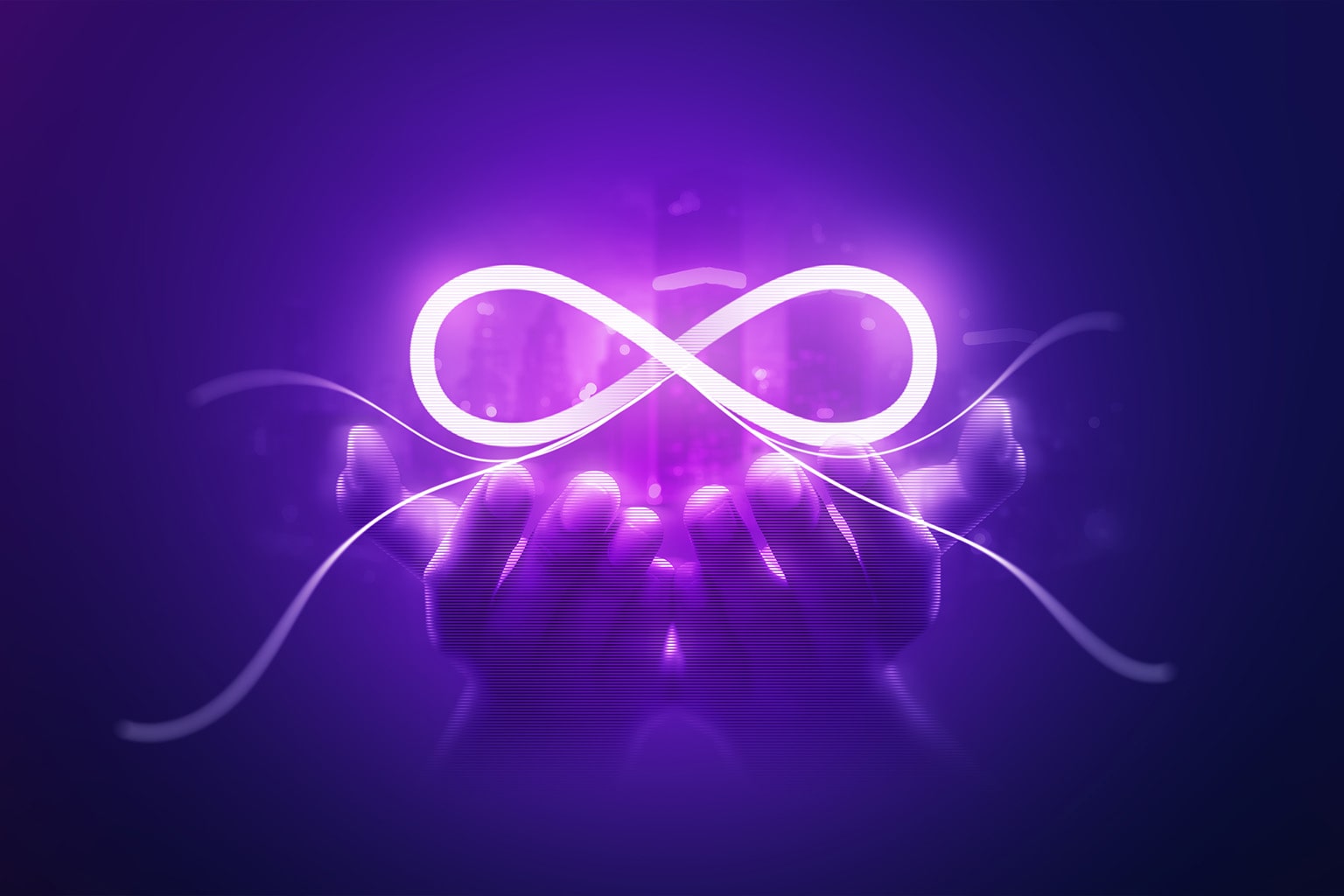
Finite and infinite capacity planning are two approaches used in production planning and scheduling, with key differences in their assumptions and methodologies.
Finite Capacity Planning
- Assumption: Finite capacity planning assumes that resources, such as labor, machines, and materials, have limitations and cannot be infinitely stretched.
- Resource Constraints: It considers the capacity constraints of various resources and ensures that the production plan aligns with the available capacity.
- Detailed Scheduling: Finite capacity planning generates schedules that consider the specific capacity of each resource, ensuring that tasks are assigned within their capacity limits.
- Realistic Timeframes: It provides more accurate estimates of production lead times by accounting for resource limitations, resulting in realistic scheduling and delivery commitments.
- Bottleneck Identification: Finite capacity planning helps identify bottlenecks in the production process, allowing manufacturers to proactively address and resolve capacity constraints.
- Complexity: Implementing and maintaining can be more complex and time-consuming due to the need for detailed resource capacity data and ongoing capacity adjustments.
Infinite Capacity Planning
- Assumption: Infinite capacity planning assumes that resources are not constrained and can handle any level of demand without limitations.
- No Resource Constraints: It disregards resource limitations and schedules tasks without considering the resources' capacity.
- High-Level Planning: Infinite capacity planning focuses on generating high-level plans and schedules without accounting for the specific capacity of resources.
- Optimistic Timeframes: It often results in optimistic estimates of production lead times since it does not consider resource constraints that may impact actual production times.
- Limited Bottleneck Visibility: Infinite capacity planning does not provide explicit visibility into bottlenecks or capacity constraints, which can lead to inefficiencies and delays in production.
- Simplicity: It is generally easier to implement and maintain than finite capacity planning since it does not require detailed resource capacity data or adjustments.
Overall, the choice between finite capacity planning and infinite capacity planning depends on the specific needs and characteristics of the manufacturing environment.
Finite capacity planning offers a more realistic and accurate approach. Still, it requires more detailed information and ongoing capacity management, while infinite capacity planning provides a simpler but less precise scheduling approach.
Manufacturing Capacity Planning Process
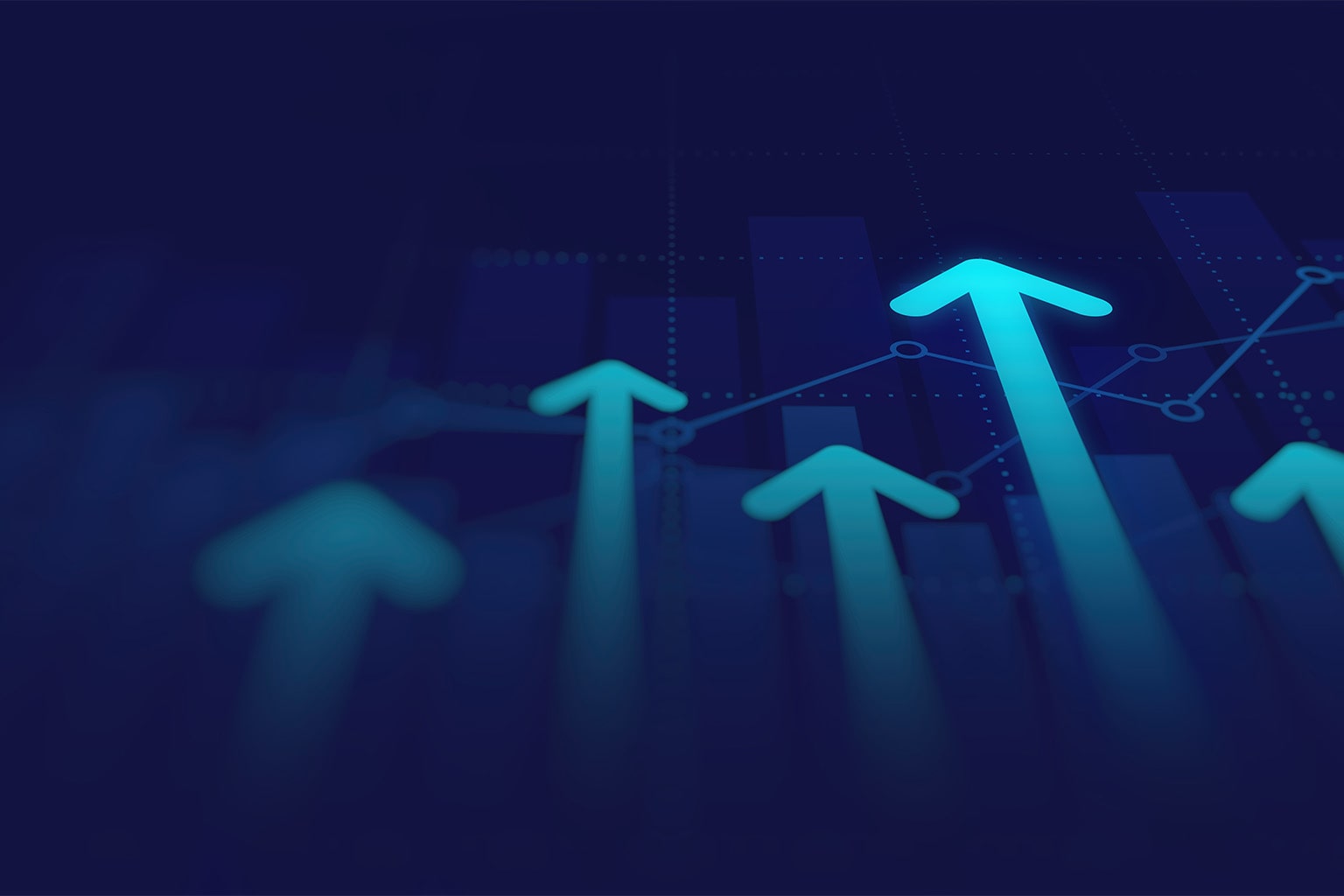
Production planning and manufacturing capacity planning involves a series of steps, each meticulously planned and executed to achieve the perfect harmony between demand and capacity.
The four fundamental steps in this process are:
- Analyzing demand
- Allocating resources
- Monitoring performance
- Adjusting capacity plans
Analyzing Demand
Analyzing demand means researching and estimating customer demand for a product or service to make informed decisions about production, cost allocation, advertising, and sales.
This process is not mere guesswork but a detailed exercise that utilizes historical data and expert advice to anticipate production requirements.
A manufacturer must fully comprehend demand trends, as this understanding forms the basis of all capacity planning decisions, shaping the strategy and influencing the allocation of resources.
Allocating Resources
The next step is allocating resources — assigning and managing resources to meet the organization's strategic objectives.
The procedure for resource allocation involves evaluating the resources available, ascertaining the objectives of the organization, and then allocating resources to tasks in a manner that optimally fulfills those objectives.
This strategic planning and management of resources can assist organizations in optimizing their resources and attaining their objectives more expeditiously.
Monitoring Performance
Performance monitoring involves assessing progress and pinpointing any impediments to the production process.
A manufacturer adjusts the capacity plan based on real-time performance data. This continuous monitoring and adjustment ensure that the manufacturing process stays on track and meets the set objectives.
Adjusting Capacity Plans
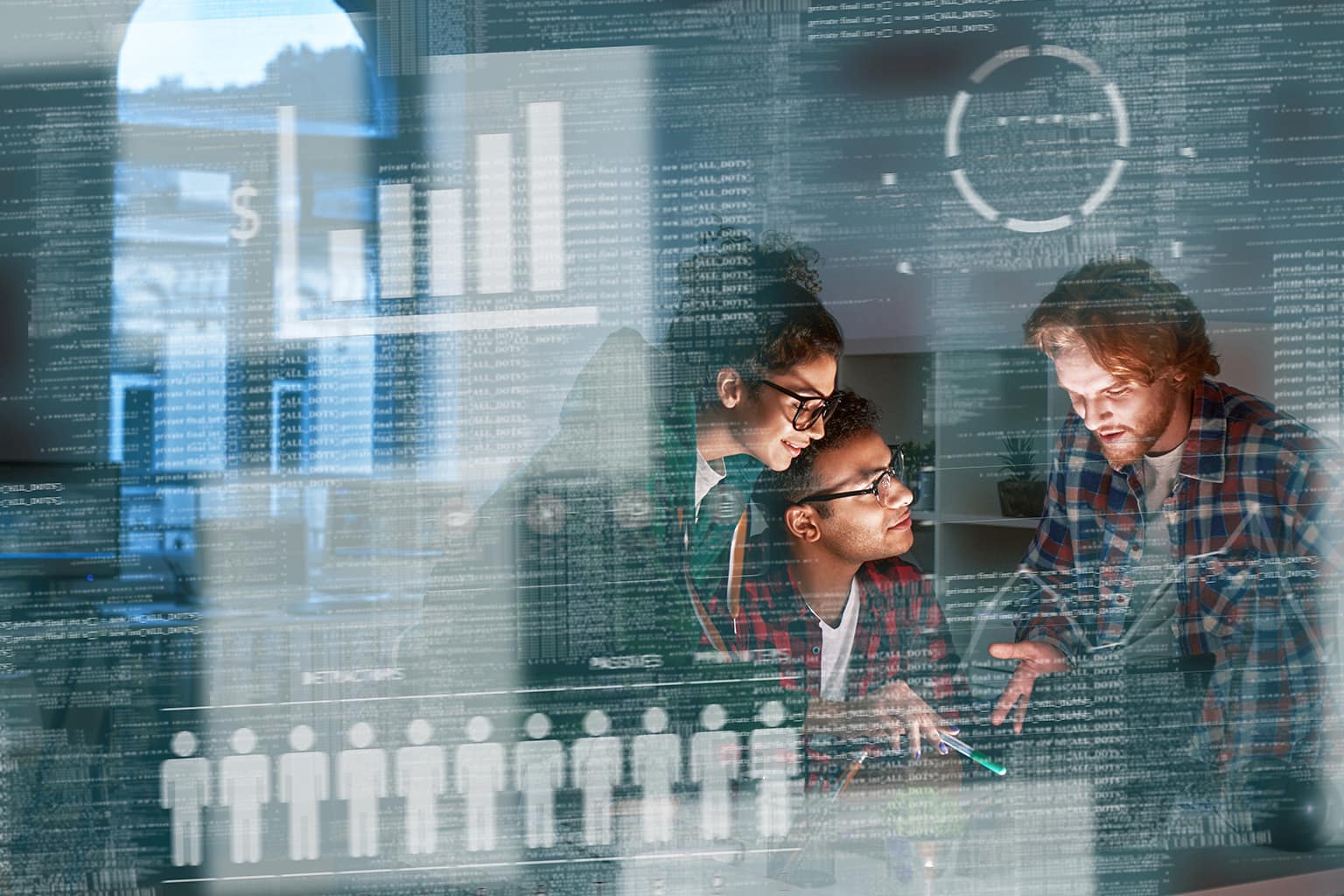
The final step in the capacity planning process involves gradually altering production capacity or demands based on prior performances.
This could mean increasing or decreasing capacity based on consumer demand or due to significant modifications to product or system architecture.
The intent of adjusting capacity plans is to guarantee that production remains on track and that resources are utilized efficiently.
Remember, a manufacturing process needs to be flexible and adaptable to meet the market's changing demands.
Three Core Strategies for Manufacturing Capacity Planning
In manufacturing capacity planning, three strategies play key roles: Lead, Lag, and Match.
The Lead strategy involves having sufficient resources to meet demand projections. The Lag strategy, on the other hand, involves having sufficient resources to fulfill demand, not estimated demand projections.
Between these two extremes lies the Match strategy. This strategy integrates the lead and lag capacity planning approaches, monitoring actual demand, demand planning estimates, and market developments to adjust capacity.
Benefits of Effective Manufacturing Capacity Planning
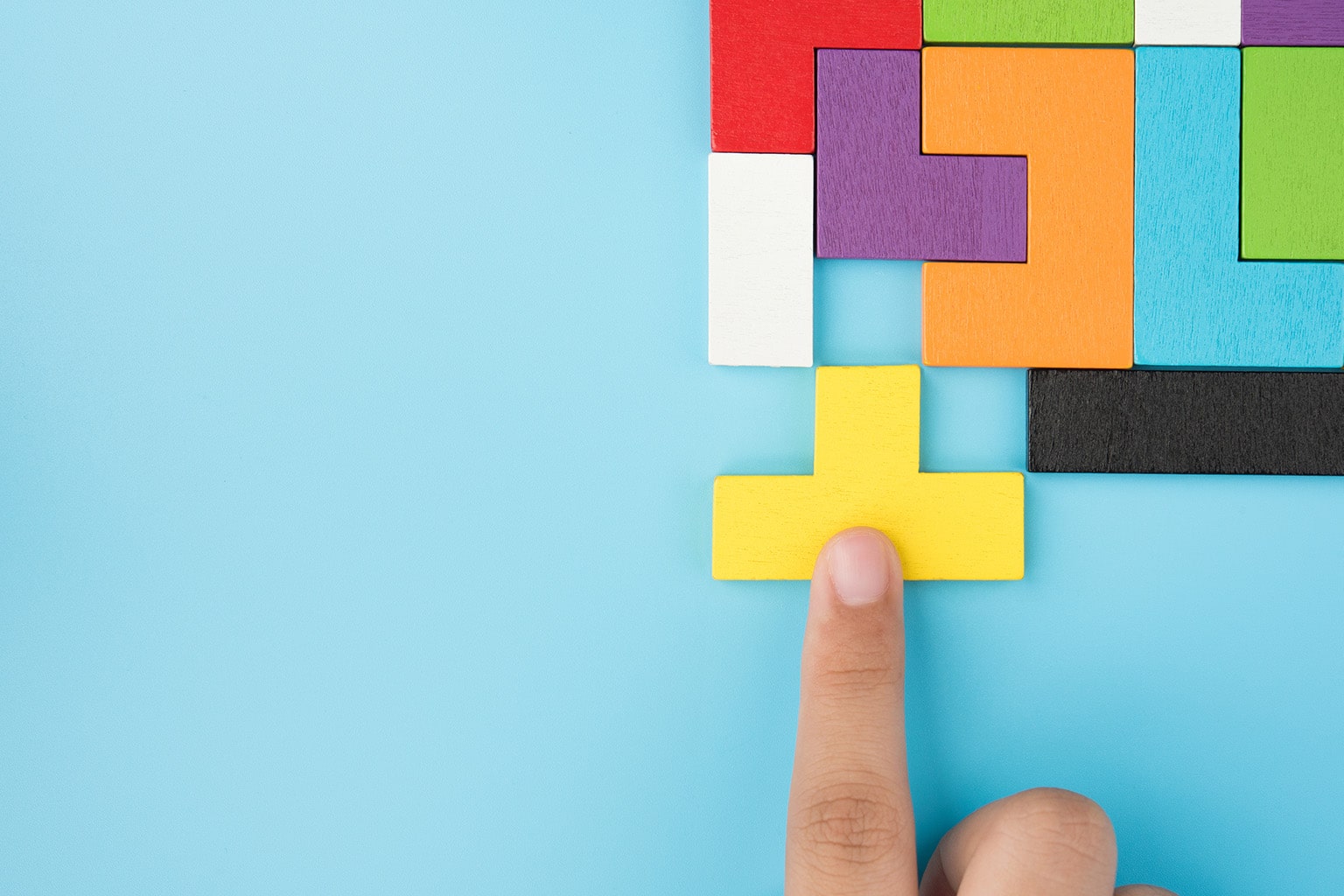
Effective manufacturing capacity planning enables businesses to anticipate and plan for any alterations in demand, optimize resources, reduce expenses, identify bottlenecks, and avert product deficiencies.
Most importantly, effective and accurate capacity planning enhances customer satisfaction by aiding businesses to fulfill customer orders on time.
Capacity Planning Tools and Software Solutions
Advanced tools like manufacturing ERP systems have revolutionized capacity planning, enhancing the planning and scheduling processes, granting complete visibility, and allowing businesses to anticipate future demand.
NetSuite ERP for Manufacturing
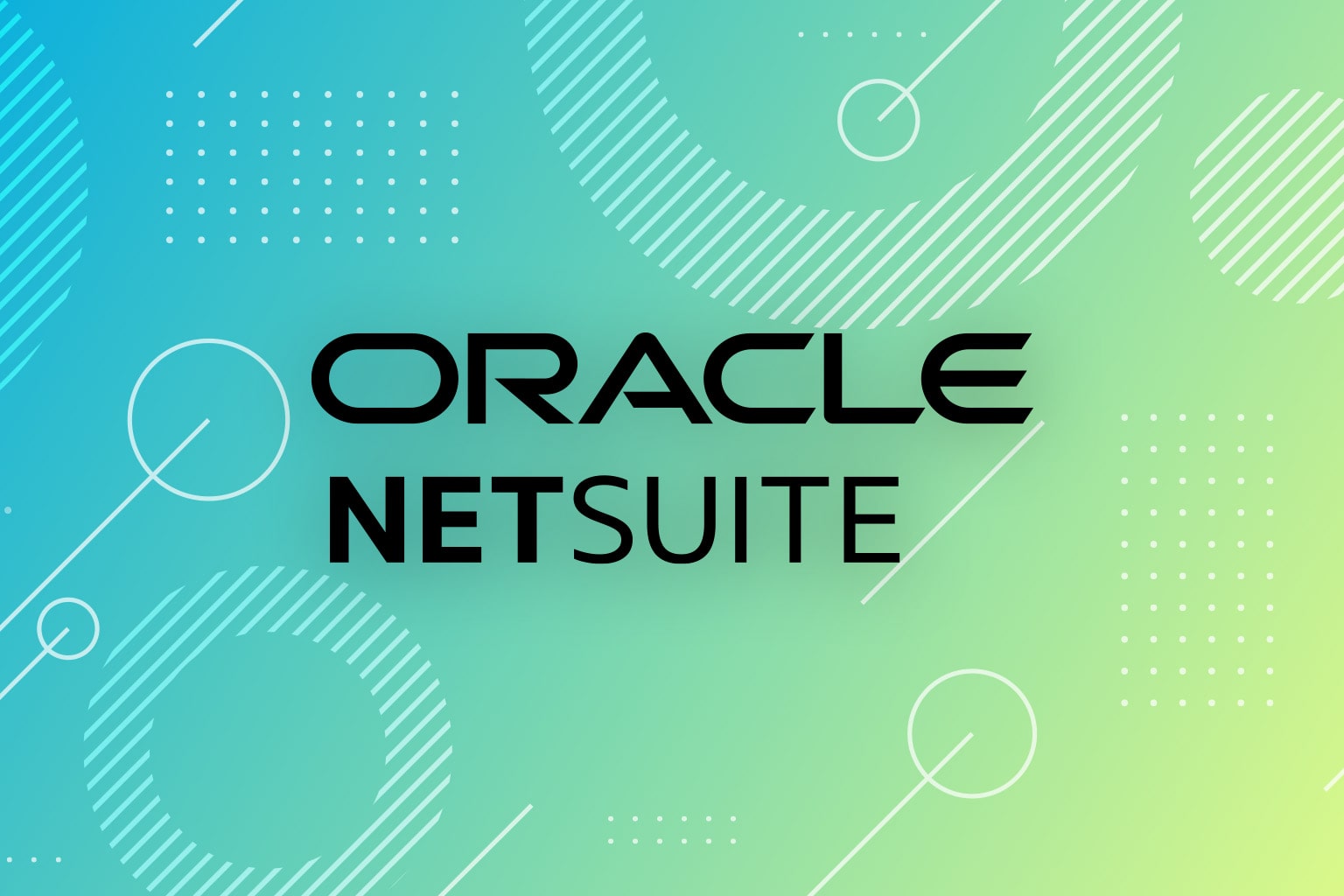
NetSuite ERP (enterprise resource planning) software is a comprehensive cloud-based solution that offers numerous benefits to manufacturing companies. The key is that NetSuite brings all your business processes and data into one system, providing a single source of truth for your manufacturing business.
It streamlines and automates critical manufacturing processes, including supply chain management, inventory and warehouse management, production planning, and financials.
The solution also facilitates seamless collaboration with suppliers and customers, enabling streamlined procurement, accurate demand forecasting, and efficient order management.
Its robust reporting and analytics capabilities provide valuable insights into performance metrics, allowing manufacturers to make data-driven decisions and continuously improve their operations.
Overall, NetSuite ERP empowers manufacturing companies with the tools and visibility needed to drive growth, enhance productivity, and maintain a competitive edge in the market.
Use Paper Street Scheduler to Manage Capacity Planning
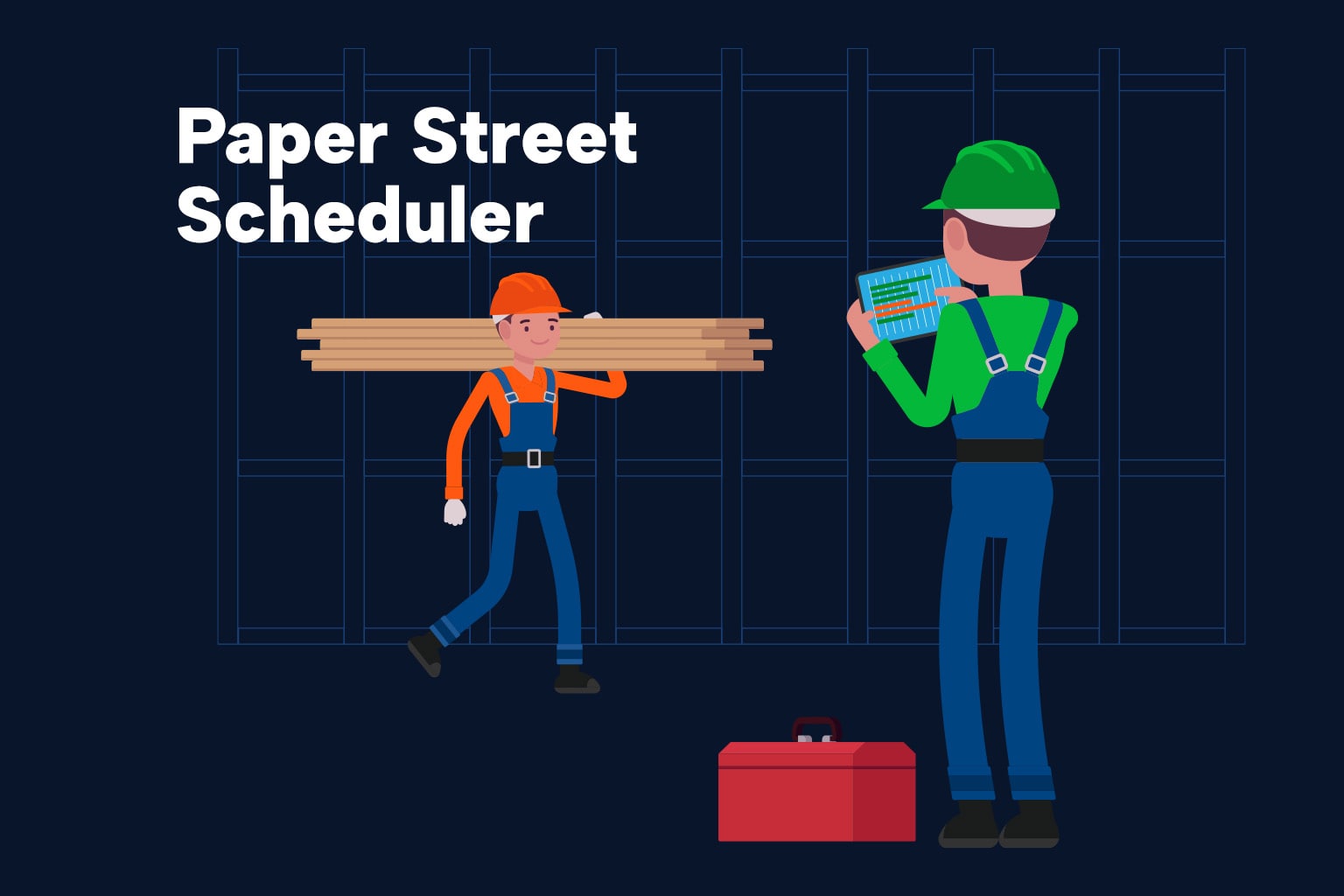
Completely control manufacturing capacity planning by adding Paper Street Scheduler to NetSuite. This tool provides drag-and-drop scheduling, capacity planning, and work order completion in manufacturing.
It’s like a digital conductor that enables you to define the production capacity required to meet product demand within a specific time frame, ensuring a seamless performance.
In addition, manufacturers can control infinite capacity planning management, finite capacity planning management, machine maintenance utilization, and divide work order operations into multiple steps.
Next Steps to Leveling Up Manufacturing Capacity Planning
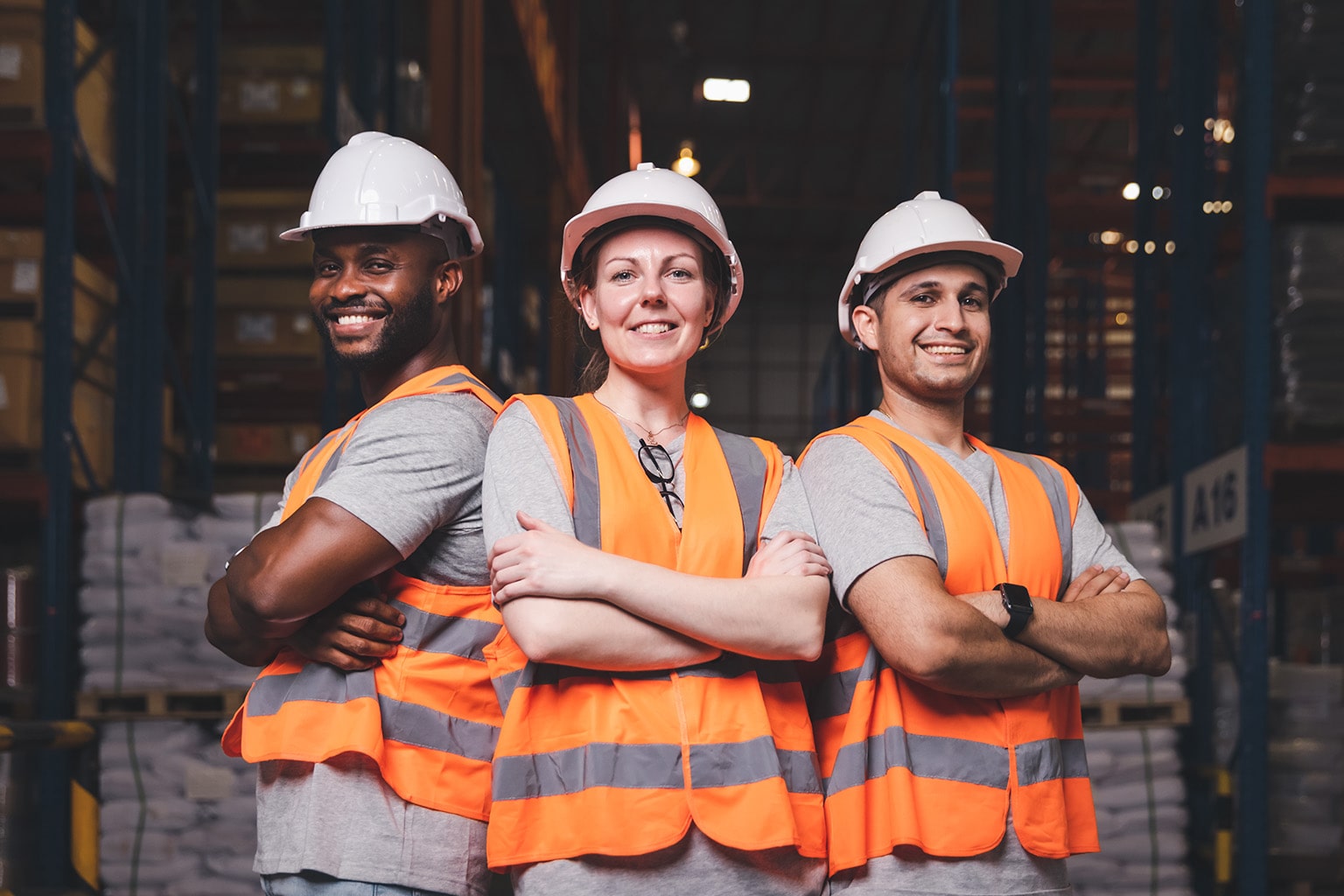
Manufacturing capacity planning is about ensuring the right resources are available at the right time to meet demand and improve the overall efficiency of the manufacturing process.
Just as a well-composed symphony leaves a lasting impression on the audience, effective capacity planning leaves a lasting impact on a business. It reduces costs, improves efficiency, enhances customer satisfaction, and ensures the business stays in tune with the market demands.
To help you implement and use the latest innovations in capacity planning with NetSuite ERP, feel free to reach out to our team of experts with a combined six decades of experience in the manufacturing industry. We’d be happy to help you grow and achieve your business goals.